The price of custom metal parts is affected by a variety of comprehensive factors:
Table of Contents
Toggle1. Material Cost
(1) Type of Metal Material
- Different metal materials have significant price differences. For example, precious metals such as gold, silver, and platinum are extremely expensive and are mainly used in high-end electronic conductive parts, jewelry, and some special industrial catalytic fields. In contrast, ordinary carbon steel has a relatively low price and is commonly used in building structural components and some mechanical parts with low performance requirements. 304 stainless steel, due to its good corrosion resistance and mechanical properties, has a moderate price and is widely used in the customization of metal parts for food processing equipment and chemical containers.
- Some rare metal materials have even higher prices. For instance, titanium and titanium alloys, with their high specific strength, excellent corrosion resistance, and biocompatibility, are widely used in the aerospace and medical device fields. However, their price is several times that of ordinary steel. This is because the extraction and processing of titanium are more difficult and the resources are relatively scarce.
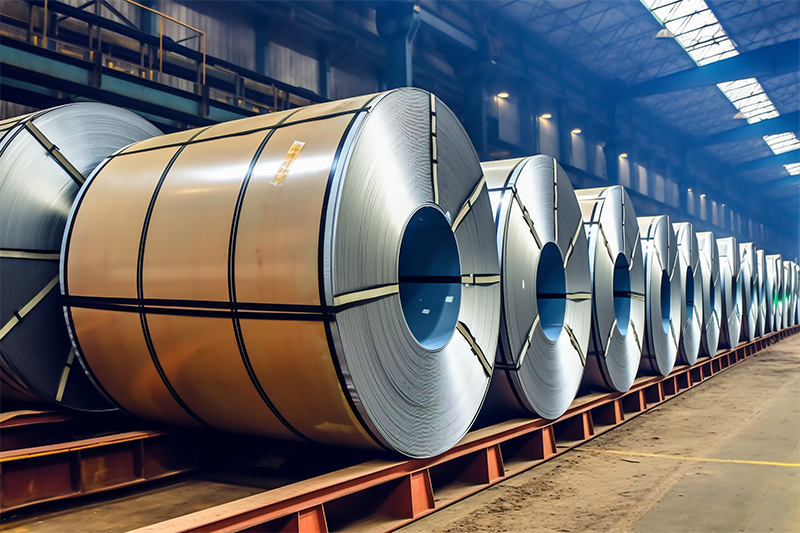
(2) Purity and Quality Grade of Materials
- High-purity metal materials usually have a higher price. Taking copper as an example, electrolytic copper with a purity of 99.99% is more expensive than copper with a purity of 99%. In the electronics industry, high-purity copper is used to manufacture high-precision circuit boards and wires to ensure good electrical conductivity and signal transmission quality.
- The quality grade of materials also affects the price. For alloy steel, it is divided into different grades according to its mechanical properties and chemical composition. High-grade alloy steel, which can withstand higher stress and temperature, naturally has a higher price than low-grade alloy steel. Such materials are often used in the manufacturing of high-performance engine parts, high-end molds, and other custom metal parts.
(3) Supply and Demand Relationship of the Material Market
- When the market demand for a certain metal material is strong and the supply is tight, the price will rise. For example, during the rapid development of the global new energy vehicle industry, the prices of lithium, nickel, and other metal materials used in the manufacturing of batteries and motors have soared. Because these metals are the key raw materials for lithium batteries and high-performance motors, and the demand has increased sharply, while the extraction and supply of resources cannot keep up with the growth rate of demand.
- Conversely, when the market supply is excessive, the price will decrease. For example, during the period of overcapacity in the steel industry, the price of ordinary steel has been continuously declining, which has also led to a decrease in the price of custom metal parts such as building structural components and ordinary mechanical parts that mainly use steel as the raw material.
2. Processing Cost
(1) Complexity of Processing Technology
- Complex processing technologies will increase costs. For example, using 3D printing technology to produce metal parts, due to the high cost of equipment, special printing materials, and the need for fine parameter control during the printing process, its processing cost is higher than that of traditional casting or machining processes. 3D printing can create metal parts with complex internal structures, such as aero-engine blades, with complex cooling channel designs to improve engine performance, but this complex manufacturing method is costly.
- For precision-machined metal parts, such as high-precision optical instrument components and aerospace parts, high-precision processing equipment (such as five-axis linkage machining centers) and advanced cutting tools are required, and extremely high requirements are placed on dimensional accuracy and surface roughness during the processing. These factors lead to a significant increase in processing costs because high-precision processing equipment is expensive, has high maintenance costs, and has relatively low processing efficiency.
(2) Precision Requirements of Processing
- The higher the precision requirements of metal parts, the higher the processing cost. For example, in the manufacturing of precision bearings, the tolerance requirements for the diameter and roundness of the inner and outer rings are extremely strict, often within a few microns. Achieving such high precision requires multiple processing steps and strict quality control, which significantly increases the processing cost. High-precision machining not only requires advanced equipment but also highly skilled technicians and a large amount of time and effort for measurement and adjustment.
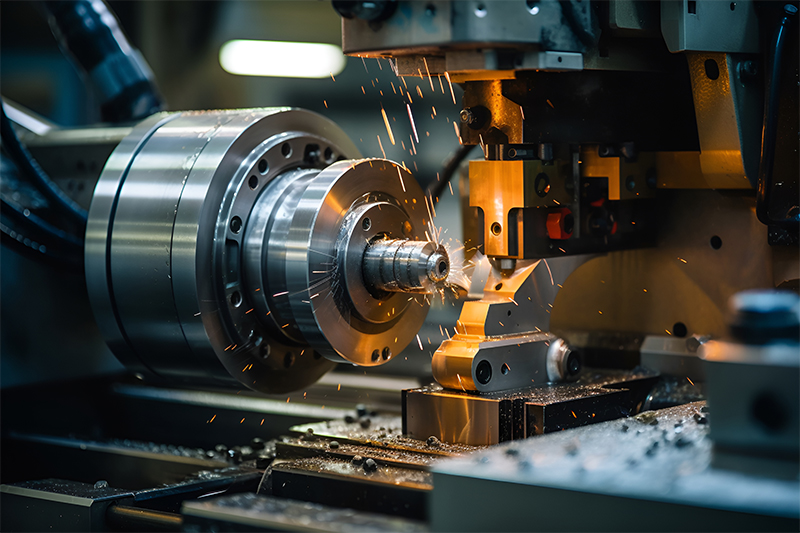
(3) Quantity of Customized Parts
- The quantity of customized metal parts also has an impact on the unit price. Generally, the larger the order quantity, the lower the unit processing cost. This is because when the production volume is large, some fixed costs such as equipment setup, mold making (if applicable), and programming can be 摊薄 over more parts. For example, in the mass production of automotive metal parts, the unit price of a single part can be much lower than that of a small-batch customized order. However, for very small quantities or prototype production, due to the inability to achieve economies of scale, the unit price may be relatively high.
3. Surface Treatment and Finishing Cost
- Surface treatment and finishing processes can also affect the price of custom metal parts. Common surface treatments include electroplating, anodizing, painting, powder coating, etc. The cost of electroplating with different metals varies. For example, chrome plating is often used to improve the appearance and corrosion resistance of metal parts, but the cost of chrome plating is relatively high due to the price of chromium and the complexity of the electroplating process. Anodizing is widely used for aluminum parts to enhance their surface hardness and corrosion resistance. The price of anodizing depends on factors such as the thickness of the anodized layer and the color requirements. Painting and powder coating are mainly used for decorative and protective purposes, and their costs are related to the type of paint or powder, the number of coating layers, and the complexity of the spraying process.
4. Design and Engineering Cost
- If the customer requires a unique and complex design, additional design and engineering costs will be incurred. Designing metal parts with special shapes or functions requires the use of professional design software and the expertise of engineers. For example, in the design of custom metal enclosures for high-end electronics, considerations such as heat dissipation, electromagnetic shielding, and ease of assembly need to be taken into account, which requires a lot of design work and simulation analysis. The more complex the design, the more time and effort required from the design team, and thus the higher the cost. In some cases, if the customer only has a rough concept and requires the manufacturer to provide complete design services, the design cost will be even more significant.
5. Tooling and Die Cost
- For some metal parts that require the use of molds or special tooling for production, the cost of tooling and die making is an important factor affecting the price. For example, in the stamping production of metal sheets to make automotive body parts, the cost of making the stamping die can be very high. The price of the die depends on its complexity, size, and precision requirements. Larger and more complex dies require more materials and advanced manufacturing techniques, resulting in higher costs. Moreover, the lifespan of the die also affects the overall cost. If the production volume is large and the die needs to be replaced frequently, the tooling cost per part will increase. In some cases, if the customer’s order quantity is small and cannot fully utilize the lifespan of the die, the manufacturer may need to amortize the die cost over a smaller number of parts, leading to a higher unit price.
In conclusion, the price of custom metal parts is determined by a combination of multiple factors related to materials, processing, surface treatment, design, and tooling. Customers and manufacturers need to comprehensively consider these factors to ensure that the price is reasonable and meets the requirements of both parties in the customization process.