The surface treatment methods of custom metal parts have a significant impact on the price.
Table of Contents
Toggle1. Cost Differences among Different Surface Treatment Methods
Electroplating
- Electroplating is a common surface treatment method that deposits a layer of metal film on the metal surface through electrolysis. Its price is affected by the type of electroplated metal. For example, chrome plating can provide a bright and corrosion-resistant surface for metal parts. However, the price of chrome plating is relatively high because chromium is a relatively expensive metal, and the electroplating process requires strict control of parameters such as current density and plating time to ensure the quality and thickness of the plated layer. Nickel plating is also widely used, and its price is generally lower than that of chrome plating but still adds a certain cost to the metal parts. Gold plating, due to the high price of gold, is only used in some high-end or special applications where excellent conductivity and aesthetics are required, and the cost of gold plating is extremely high.
Anodizing
- Anodizing is mainly used for aluminum and its alloys. It forms an oxide layer on the surface of the metal through an electrochemical reaction, which can improve the hardness, corrosion resistance, and wear resistance of the surface. The cost of anodizing is related to factors such as the thickness of the anodized layer and the color requirements. Thicker anodized layers usually require longer processing time and more chemicals, so the cost is higher. If special colors are required, additional coloring agents and more complex processing steps may be needed, which will also increase the cost. For example, a standard clear anodized finish may have a relatively lower cost, while a custom-colored anodized finish with a specific shade and high colorfastness will be more expensive.
Painting and Powder Coating
- Painting involves applying a liquid paint layer on the metal surface. The cost of painting depends on the type of paint used. High-quality paints with good weather resistance, adhesion, and gloss, such as automotive-grade paints, are more expensive. The number of paint layers also affects the price. Multiple coats of paint are often required to achieve better protection and appearance, which increases the cost. Additionally, if special finishes like metallic or textured finishes are desired, it may require more complex painting techniques and additional materials, further increasing the cost.
- Powder coating is a dry coating process where a powder is electrostatically applied to the metal surface and then cured. The cost of powder coating is related to the type of powder, such as epoxy, polyester, or hybrid powders. Epoxy powders are known for their good corrosion resistance, while polyester powders offer better weatherability. The price of different powders varies, and the complexity of the coating process, such as the need for pre-treatment of the metal surface to ensure good adhesion, also affects the overall cost.
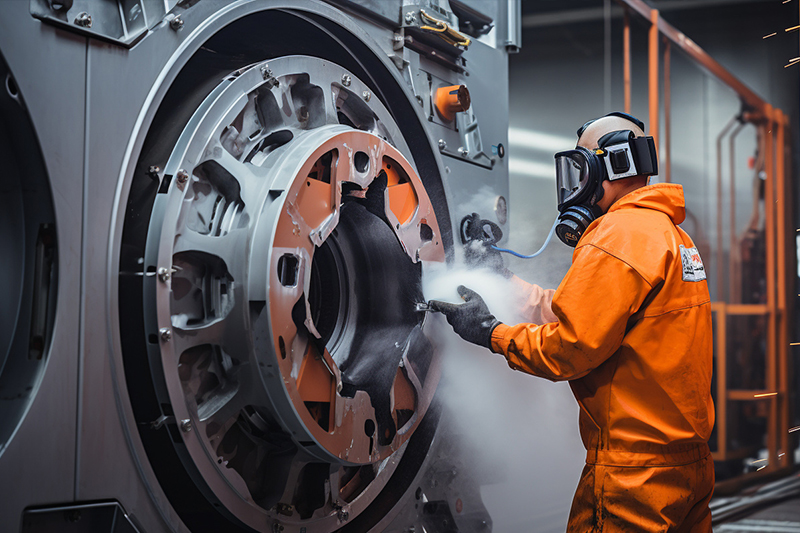
2. Impact of Surface Treatment Complexity on Price
Masking and Multiple Treatment Areas
- If a metal part requires masking certain areas during surface treatment to achieve a specific pattern or design, it adds to the complexity and cost. For example, if a metal logo or decorative pattern needs to be left untreated while the rest of the part is plated or painted, precise masking is required. This involves additional labor and materials for the masking process, and any errors in masking can lead to defective parts and rework, increasing the overall cost.
- When a metal part requires multiple different surface treatment methods in different areas, the cost also rises. For instance, one part of the metal component may need anodizing for better wear resistance, while another part requires plating for conductivity. Coordinating and performing these different treatments accurately and without cross-contamination requires more advanced equipment, skilled labor, and careful process control, all of which contribute to a higher price.
Surface Preparation Requirements
- Different surface treatment methods have different requirements for surface preparation. For electroplating, the metal surface needs to be extremely clean and free of oxides and contaminants. This may require processes such as degreasing, pickling, and polishing, which add to the cost. The more complex and time-consuming the surface preparation, the higher the overall cost of the surface treatment. For example, if a metal part has a rough surface and requires extensive polishing to achieve a smooth finish before plating, the cost of the polishing step alone can be significant. In the case of powder coating, proper surface roughening or chemical treatment may be needed to ensure good adhesion of the powder, and these additional surface preparation steps increase the cost compared to a simple cleaning process.
In conclusion, the surface treatment method and its complexity have a direct and significant impact on the price of custom metal parts. Customers need to consider their requirements and budget carefully when choosing a surface treatment option, and manufacturers should accurately assess and price the surface treatment based on these factors to ensure a fair and reasonable cost for both parties.